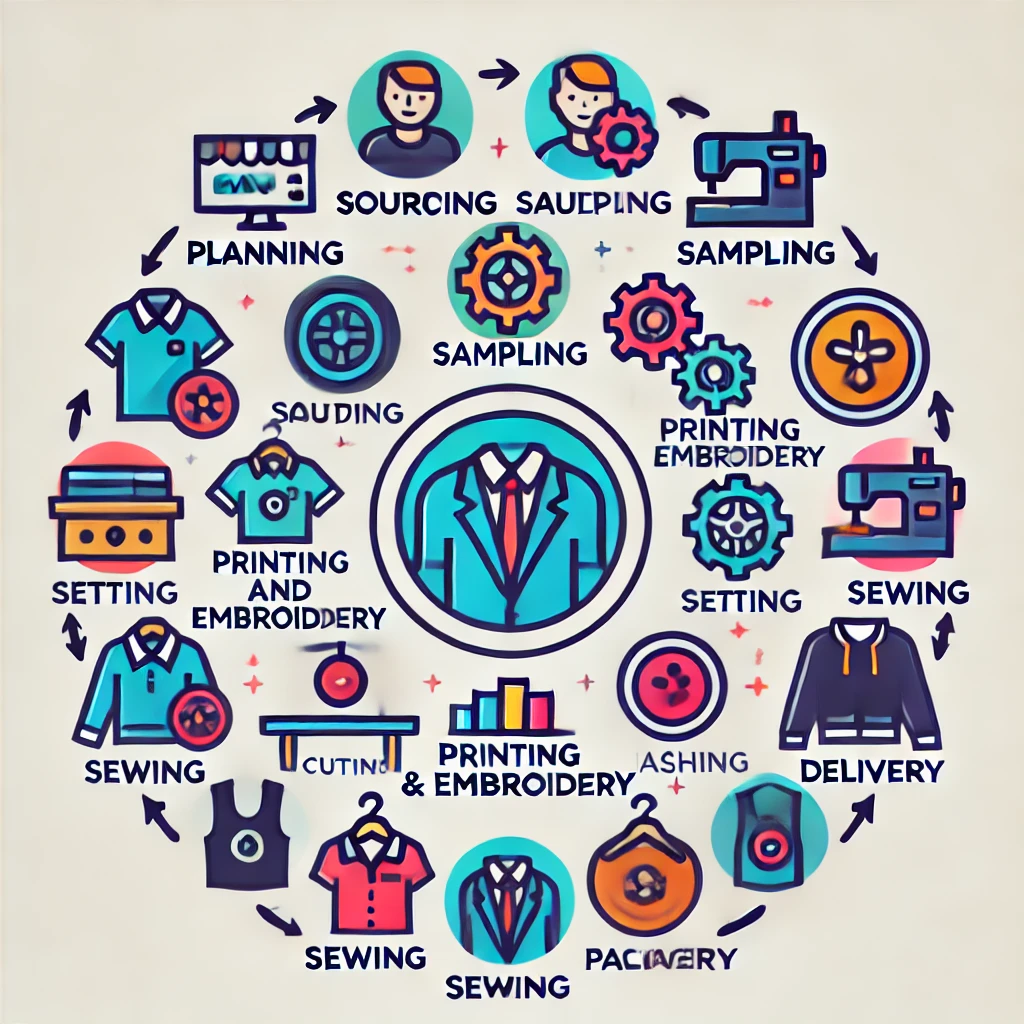
Turkey Garment Manufacturer
Collaborating with a Garment Manufacturer in Turkey
At Garment Manufacturer in Turkey, we prioritize high-quality production and customer satisfaction. Throughout our collaboration, we focus on transparency and communication at every step.
Here’s how we work:
- First, you can reach out to us to share your needs. By providing product images, technical files, and order quantities, we can offer you a customized pricing quote. The minimum order quantity (LOW MOQ) for production is 200 (recommended) pieces per model and color. Once you place your order, we can provide a free sample production.
- After you approve the sample, we move on to the production process, ensuring quality at every stage. Once production is complete, your products will be delivered within the agreed timeframe. Lastly, after delivery, we are happy to receive any feedback and look forward to working with you on future projects.
We aim to offer solutions that best meet your needs by working closely with you at every stage. We look forward to collaborating with you! Contact us to get a quick price quote.
FAQ – Got Questions? Find Answers Here
As a low moq textile manufacturer in turkey , startups may ask detailed questions to understand your production processes, pricing, quality control, and sustainability practices. Key areas of inquiry may include your production capacity and flexibility, cost optimization strategies, raw material sourcing, quality assurance methods, and logistical processes. Startups are also likely to inquire about your use of innovative technologies, your commitment to ethical and sustainable manufacturing, and how you support custom product development. Additionally, they may seek information about your ability to scale production and establish long-term partnerships as their business grows. Providing clear answers to these detailed questions can help foster strong, transparent collaborations with startup companies.
1- How to Get a Price Quote
You can send us the product image, technical file and detailed information about your request via e-mail or WhatsApp.
Define Your Product Requirements: Clearly define the product you want to produce. Include details such as fabric type, design, colors, sizes, and any special features.
Quantities: Determine how many products you want to order.
Quality Standards: If you have specific quality or certification requirements (e.g. eco-friendly, GOTS certified, etc.), specify them.
Delivery Terms: Provide information about your preferred delivery dates and logistics requirements (e.g. shipping to a specific country or warehouse).
Budget: If you have a specific budget, please let us know so we can tailor our recommendations accordingly.
Production Capacity and Flexibility ?
How do you scale your production capacity? For example, do you use additional production lines or increase labor to handle larger orders? We can flexibly scale our production capacity in line with demand. To meet larger orders, we use strategies such as installing additional production lines and increasing production line efficiency. We can also achieve higher production capacity by increasing the workforce and the number of shifts. When needed, we automate processes and increase production speed using technology.
How do you adjust your production capacity for custom orders? For instance, how do you handle design customization or small batch productions? For special orders, we adjust our production capacity according to the demands. We provide flexibility for design customizations or small batch production. In such projects, we determine the special design and production requirements in close communication with the customer. We manage small batch production independently from the main production line and can use more specialized equipment or processes for these productions.
What is the process for moving from prototype production to mass production, and what are the biggest challenges you face in this transition? The transition from prototype production to mass production requires careful planning. During the prototype phase, we test all design and quality requirements of the product. During the transition to mass production, we standardize the production process and apply quality control methods. The biggest challenge we face in this transition is to constantly maintain the desired quality in the production process and minimize potential errors. For this purpose, we perform continuous inspections and small-scale test production.
How do you handle urgent orders? What steps do you take when there is a need for expedited production or delivery? When urgent orders arrive, we first review our production plan and quickly allocate resources for these orders. When expedited production is requested, we can make shift arrangements to shorten the duration of current projects by using the flexibility in the production line. We also coordinate with the logistics and transportation departments to increase the speed of delivery. We have a predetermined action plan for such emergencies.
Quality Control and Product Testing?
What are the quality control stages in your production process? How do you ensure product quality at each step of production?
How do you maintain quality in high-volume production? What methods do you use to minimize defect rates in large batches?
How do you ensure raw material quality before production starts? What types of testing do you perform on materials?
When product defects are detected, how do you address them? What is your process for handling product returns or replacements?
Costs and Pricing ?
What methods do you use to optimize production costs? How do you control costs across raw materials, logistics, and labor?
What factors do you consider when determining pricing? Do you adjust prices based on market demand, raw material costs, or labor expenses?
How do production costs change over time? What steps do you take to minimize cost increases in response to inflation or supply chain fluctuations?
Do you offer pricing flexibility for startups? For example, do you have pricing models that accommodate small or low-budget projects?
Supply Chain and Material Sourcing?
What measures do you take to mitigate supply chain disruptions? Do you have contingency plans for raw material shortages or supplier delays?
How do you source sustainable materials and create an eco-friendly supply chain? Do you work with certified suppliers for sustainable products?
What criteria do you use when selecting suppliers, beyond quality and reliability? Do you consider ethical practices, labor rights, or environmental impact in your supplier choices?
Do you source materials locally or internationally? How do you manage customs and logistics when sourcing from overseas?
Special Sample Product Development ?
How do you handle custom design requests from startup companies? For example, if a startup asks for custom prints or fabric types, what is the process to accommodate those needs? Special design requests from you are first evaluated in detail. In the meetings held with you, the desired special prints, fabric types and other design requirements are determined. Your designs are checked and recommendations are made on fabrics, printing techniques and special workmanship details suitable for your requests. During this process, the quality of the materials to be used, aesthetic harmony and functionality are taken into consideration. For special print or fabric requests, sample production is made after design and material approval. This sample is subjected to quality control tests before being delivered to the customer.
How long does it take to create prototypes or samples? How do changes in the prototype stage translate into mass production? Sample production is usually completed within 5-10 business days. This time may vary depending on the complexity of the design and the speed of supply of the materials used. Every change in the prototype phase is carefully evaluated. Changes to be made to the design in line with your feedback are prepared as a prototype again before being included in the production process. Changes are made in a way that preserves quality and functionality. If requested by you, after receiving the prototype and final approval, production processes are standardized for the transition of the design to mass production. Every change made to the design is also integrated into quality control processes.
What level of support do you provide during the product design phase? Do you collaborate with clients on design concepts and provide feedback during the process? During the sample phase, continuous feedback is provided by working closely with you. Different alternatives can be presented on the sample and revisions can be made in line with your expectations. Technical guidance is provided to you during the sample process. This can be about choosing the right fabric, printing techniques or cutting methods. During the sample phase, the first prototype is sent to you, then when approval is received, the production phase is started.
6- Delivery and Logistics ?
What is your typical lead time for orders after production? How do you handle logistics for both domestic and international deliveries? For countries near Turkey, the delivery time is usually between 7-10 business days after production is completed. For deliveries to Farther Away Countries, this time may vary depending on the destination country and is usually between 10-20 business days. Delivery times may vary depending on the size of the order, product features and shipping options.
How do you address delays in the logistics process? What steps do you take to ensure on-time delivery and minimize shipping disruptions? Logistics delays are usually minimized by maintaining constant communication with transportation partners. Since we usually work with DHL, Fedex and UPS, there may be a delay of 1-2 minutes with these types of express shipping companies. Orders are tracked according to the predetermined delivery schedule and in case of any disruption, alternative routes are investigated.
Do you offer different shipping options for customers? For example, expedited or international shipping, and what are the associated cost differences? Free, Standard, expedited (express) and economical alternatives. Expedited shipments usually require higher shipping costs. These options may be offered at different prices for domestic and international shipping. Depending on customer preferences, for example, air shipping for urgent orders, and road or sea shipping for economical options may be recommended. We also have a Door-to-Door Delivery Service.
How do you ensure the safety and integrity of products during shipping? What packaging and transport methods do you use to prevent damage? Durable, damage-proof packaging is used to ensure the safety of the products. Each product is packaged in a high-quality cardboard box to protect against scratches or crushing. In addition, sturdy palletizing methods and appropriate load balancing are used to ensure the stability of the products during transportation. Each package is insured against damage that may occur during transportation. (for door-to-door delivery option)
7- Innovation and Technology Usage ?
What new technologies and manufacturing methods do you incorporate into your production process (e.g., digital printing, 3D fabric design, automated production lines)? How have these technologies improved your operations? As a Garment Manufacturer in Turkey, we are constantly working on improving our production processes and making them compatible with modern technologies. We can achieve faster and more detailed prints using digital printing technology. In addition, we can design more innovative and aesthetic products with 3D fabric design. Automatic production lines increase our production speed and provide error-free production processes. These new technologies have helped us increase operational efficiency as well as improving our product quality.
How do you stay updated on the latest innovations in the textile industry? How do you integrate advancements such as smart fabrics or eco-friendly manufacturing techniques into your operations? As Turkey Garment Manufacturer, we participate in sector fairs, conduct research and work closely with suppliers that offer innovative solutions to follow the latest innovations in the textile industry. We integrate developments such as smart fabrics and environmentally friendly production techniques into our operations by researching best practices and new technologies in the sector. Incorporating these innovations into our production processes helps us both reduce our environmental impact and provide a competitive advantage.
Do you use automation in your production processes? If so, how does automation impact production speed and quality? Yes, as Garment Manufacturer in ISTANBUL, we use ERP Production system tracking software in our production processes. Automation increases our production speed and ensures continuous quality. We minimize error rates and make production processes more efficient by using automatic machines, especially in cutting and sewing processes. This both saves time and enables large orders to be completed quickly.
Do you use digital design and production software? If so, how do these tools support your design and manufacturing workflows? Yes, we use Production software. This software digitizes our production workflows and allows us to accurately manage all the data required to produce error-free and more customized products. In addition, thanks to the software, we can offer high-quality and unique products to our customers in shorter periods of time.
8- Sustainability and Ethical Manufacturing ?
What steps are you taking to ensure sustainable textile production? For example, do you use organic materials, oeko-tex waste management strategies, or energy-efficient processes? We have a great commitment to sustainable textile production. We take care to use organic and natural materials in our production processes. At the same time, we ensure that the raw materials used are from sustainable and certified sources. Our waste management strategies include the use of recycled fabrics and waste materials. We continuously optimize the production process to minimize waste. We also use innovative technologies and machines for energy-efficient production processes.
How do you minimize the environmental impact of your manufacturing facilities? What steps have you taken to implement waste recycling, energy-saving measures, or low-emission technologies? We implement a number of strategies to reduce the environmental impact of our production facilities. We deliver waste to recycling facilities weekly and recover material waste from textile production. We use energy-efficient machinery to save energy and invest in renewable energy sources such as solar energy. We also try to minimize our carbon footprint by optimizing our production processes with low-emission technologies. We also monitor water usage and develop solutions that minimize water consumption.
9- Long-Term Partnerships and Strategic Collaborations ?
What do you look for when forming long-term partnerships with startup companies? How do you approach building a strategic partnership with growing brands? When establishing long-term partnerships with start-ups, we prioritize trust and open communication. Understanding and contributing to the growth of start-ups is our priority. We approach our partnerships with flexibility, on-time free delivery and a commitment to quality. We also try to understand the long-term goals of our business partners or start-ups and suggest solutions that will add value to them. As a brand grows, we focus on developing together to maintain flexibility and a supportive approach in high-quality production processes.
How do you scale production to meet the growing demands of startup companies? How do you manage increasing order volumes as a customer’s business expands? While establishing strategic partnerships with growing startup brands, we develop appropriate strategies to increase our high-quality production capacity and maintain quality in parallel with the growth targets of the brand. Flexibility and rapid adaptation are important factors for growing brands. Therefore, we take care to provide fast and effective solutions for new designs, customizations, small-scale, large-scale orders or special needs. In addition, we constantly review and improve our production processes to adapt to the rapidly changing and updated demands of the brands.
Do you offer special support programs for startups? How do you assist new companies in scaling their production or managing initial product runs? We dynamically scale production processes to meet the growing demands of newly established clothing companies. In cases where order volumes increase, we meet the demands by flexibly increasing our production lines or optimizing production line capacity. We can also revise production schedules according to different customer requirements. We can also offer solutions such as increasing the workforce and investing in automation processes for growing demands. We work closely with the customer to quickly adapt to the growth process.